EXCERCISE OF SCHEME & CREATIVITY
Nano Carrier Driven Collagenase Inhibitor and Novel Therapeutics for Cartilage
PRESENTTissue penetrating collagenase development to inhibit cartilage degeneration and improve tissue mechanics
- Responsibilities: Design and conduct chemical reaction, evaluation of conjugation using IR, UV, NMR, evaluation of drug delivery using confocal microscope, Biomechanical test and histology.
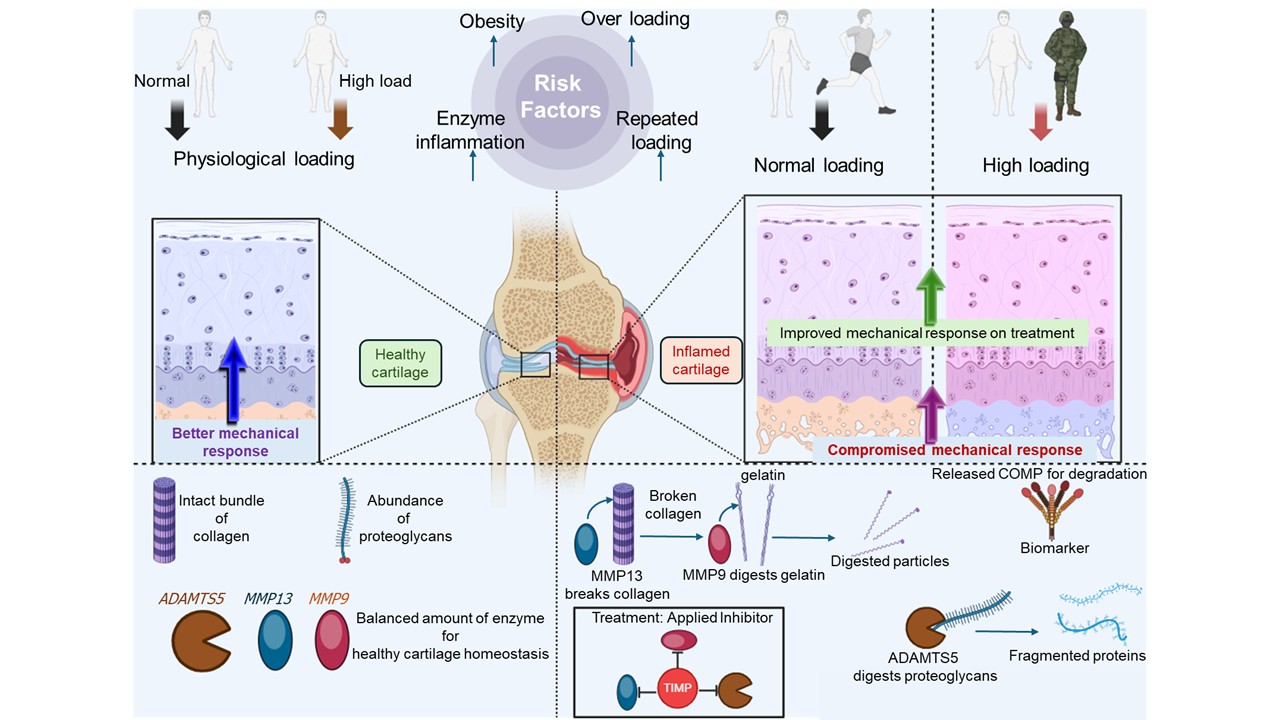
Assessment of Risk Factors on Enzyme Mediated Osteoarthritis
PresentResponsibilities: Incubation of harmful protease, protein assay, applying in-vitro risk factors (Trauma, age, obesity, site specificity) on tissue, Biomechanical test and histology.
Asst. Professor-Department of Mechanical Engineering, ULL)
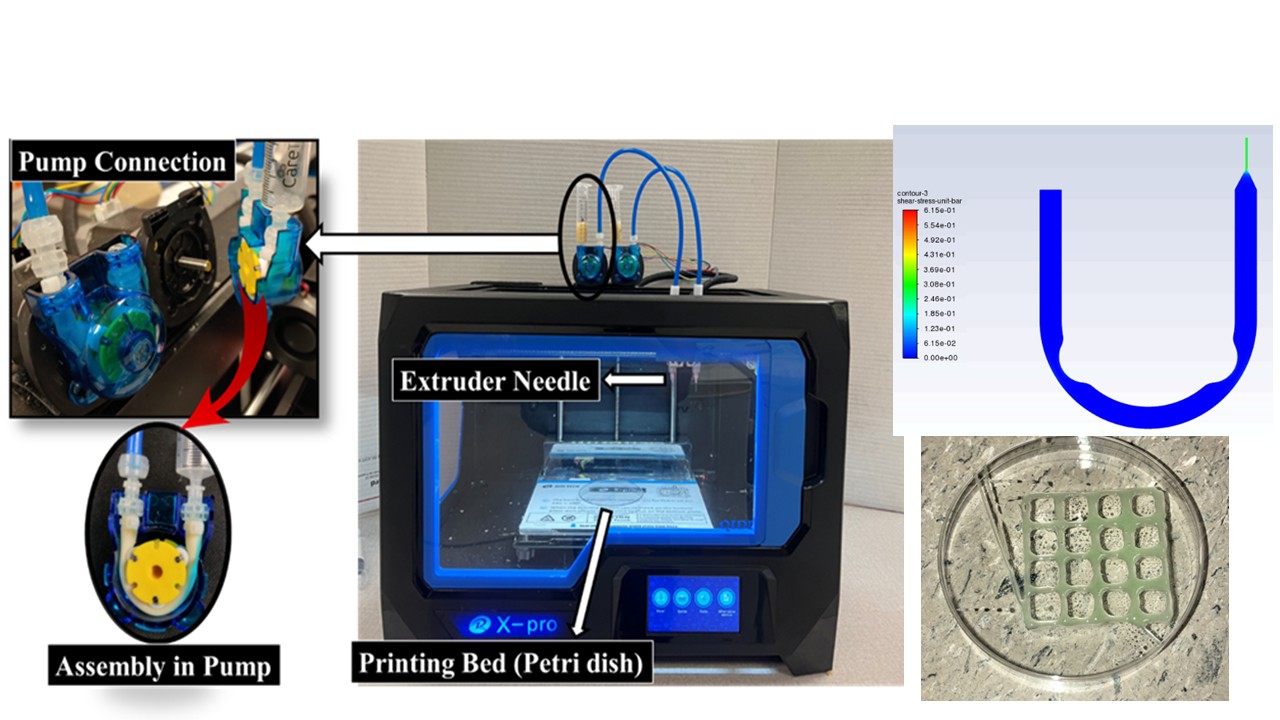
Compatible Bio-printing System for surgery
PresentTraining 7 undergrads
Responsibilities: Conceptualization, fluid dynamics simulation, manuscript writing, Hardware, System conversion, Bioink rheology
Numerical Modeling of Enzyme Mediated Cartilage
2023-2024Responsibilities: ABAQUS, FE modeling, Modeling of cell and fiber reinforced poro-elastic tissue, fitting, validation, data processing.
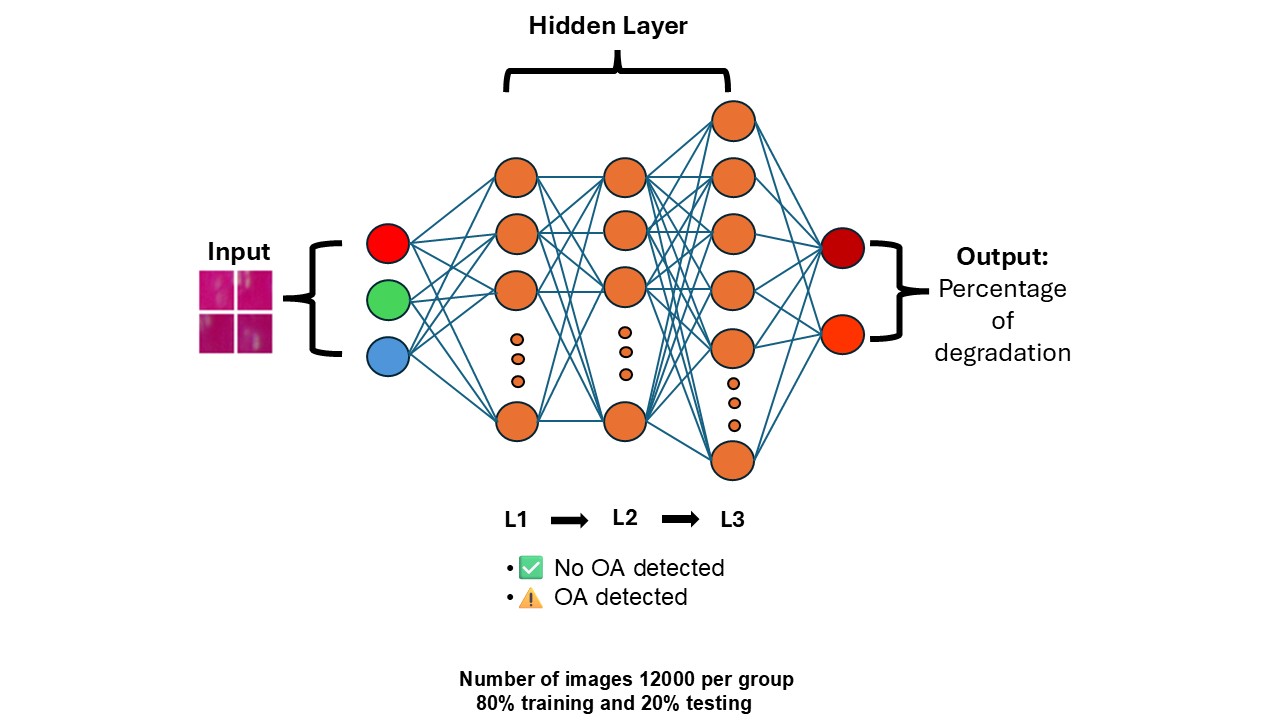
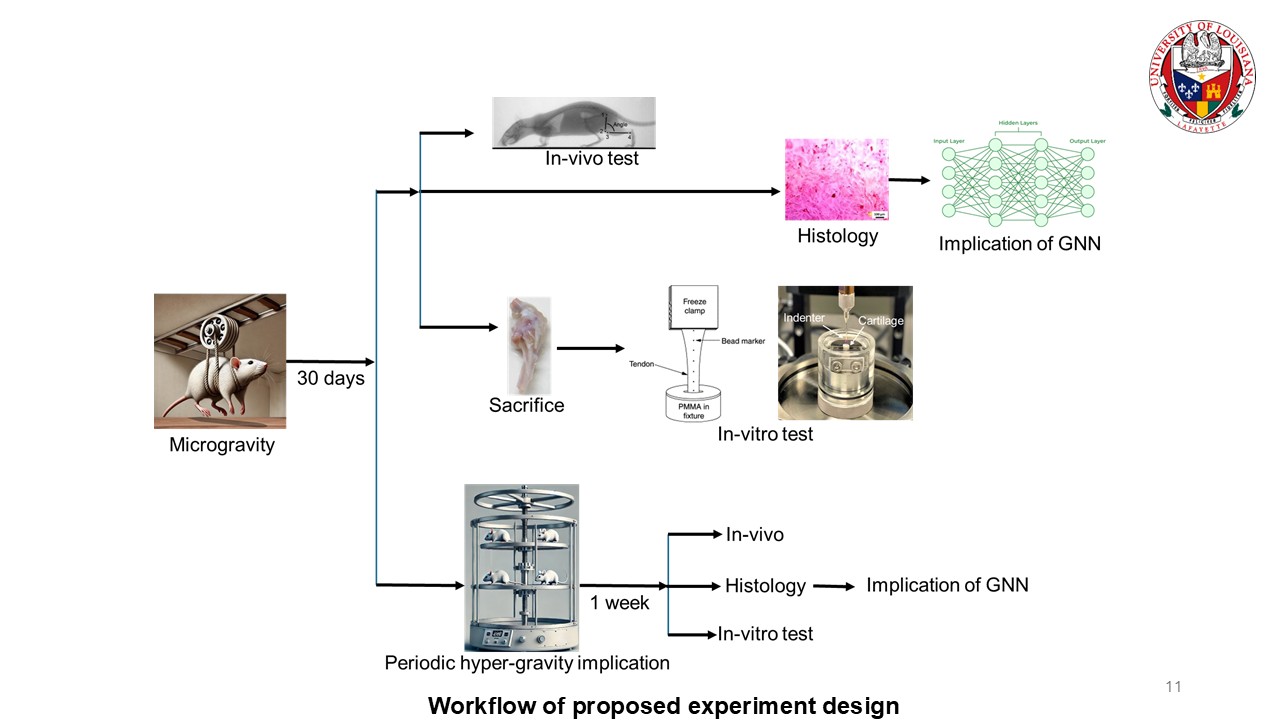
SHAPE MEMORY POLYMER FOR DEBONDABLE ADHESIVE COMPOSITE
MARCH 2021 - PRESENTThe ultimate target of this project is to develop a debondable epoxy adhesive by incorporating suitable Shape Memory Polymer(SMP) fiber in it.
- Material- Epoxy adhesive; SMPs, Aluminum substrate(5052)
- Fabrication- Steel Mold, 4D printed objects, 3d printed fixutes, Epoxy and acryric based SMPs
- Instruments-3D Printers, DOBOT Arm, Laser Cutter, UTM(Instron,KMT), DAQ with LABVIEW etc.
- Software- GOM, AutoCAD, SolidWorks(4D printing), G Code, PID, Silhouette Studio, Dobot Studio, Universal Laser System, ImageJ, National Instruments etc.
Lab Website Development
(Voluntry project)[Spring 2022(vacations)]HTML Code
A Complete Lab Website
STRUCTURAL DESIGN FOR COMPOSITE MATERIAL
(MS Project; term 1, Level 2)Code for designing composite plate to minimize weight
The model was designed to calculate maximum delfection of a multilayered composite bar. It determines the failure criterion using Tai-Hill Criterion. The optimum stacking parameters as well as the maximum failure index with respect to stacking sequence(θ,n) can be depicted from the model.
INVESTIGATION OF SOYABEAN BASED 3D PRINTABLE FILAMENT MATERIAL
SEPTEMBER 2021This additive manufacturing project will offer an eco-friendly filament for 3D printing
- Material- Soyabean shell powder, polyethylene pellets
- Fabrication- Steel Mold, Sample Size- ASTM 638(Type-V)
- Instruments- Heat Press, Filament Extruder(filamet dia 1.5mm, initially), Moment 3D Printer
- Software- AutoCAD, SolidWorks, Simplify 3D
My Responsibilities: Feasibility of printing, fabrication of spcimens for standarized tests.
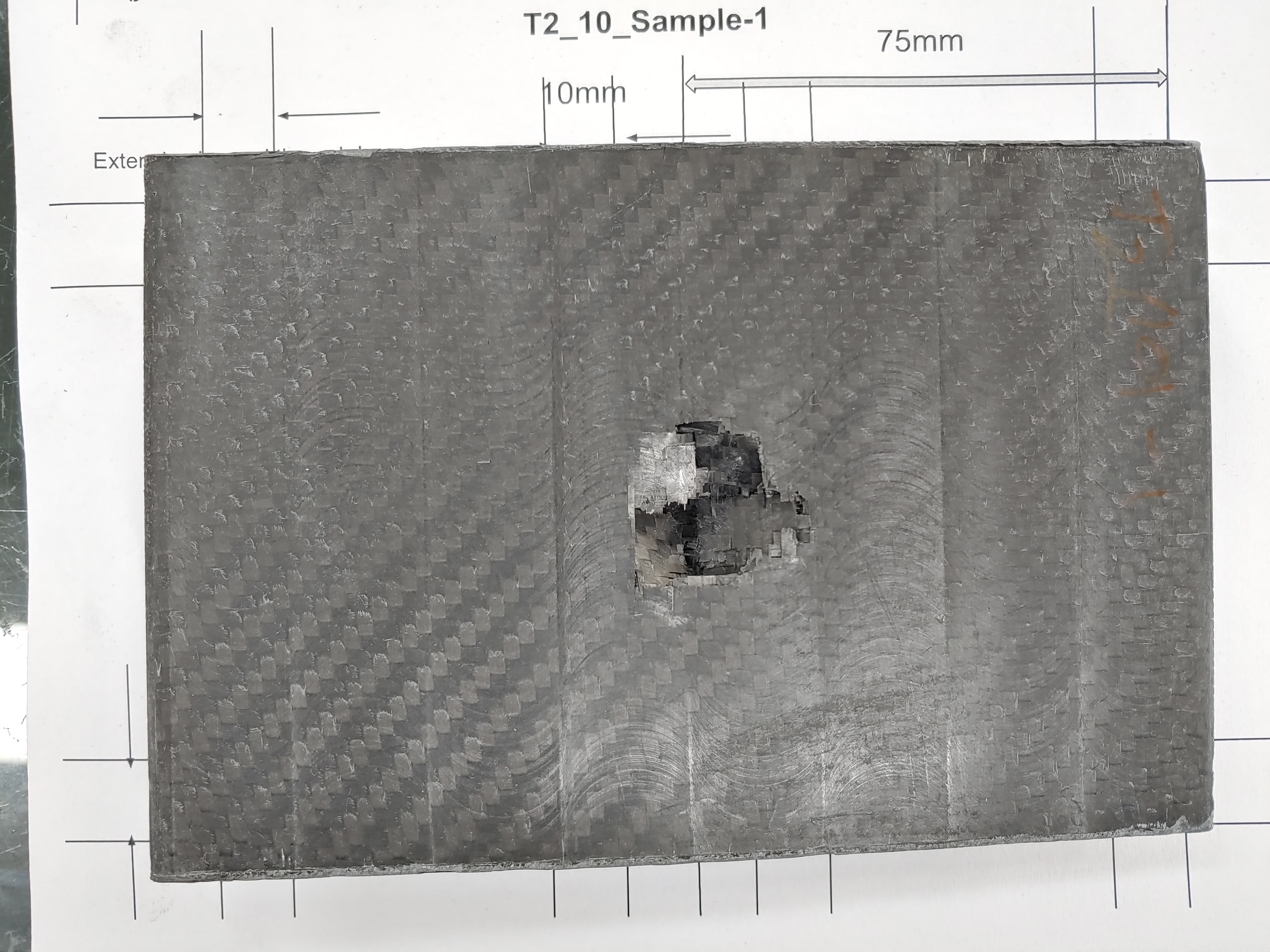
IMPACT CHARACTERISTICS OF INTERGRATED COMPOSITE PLATE
OCTOBER 2021We have fabicated fast cured piecewise integrated carbon composite plates to examine their impact characteristics.
- Material- TB Carbon PC.20B, Woven Carbon Fabric(twill weave)
- Fabrication- Steel Mold, Composite Sample Size- ASTM 7136
- Instruments- Impact Tester(Instron-ceast 9350), Lathe Machine, Heat Press, Thermal Camera
- Software- AutoCAD, Instron Bluehill Impact, ImageJ, Origin 2021, FLIR
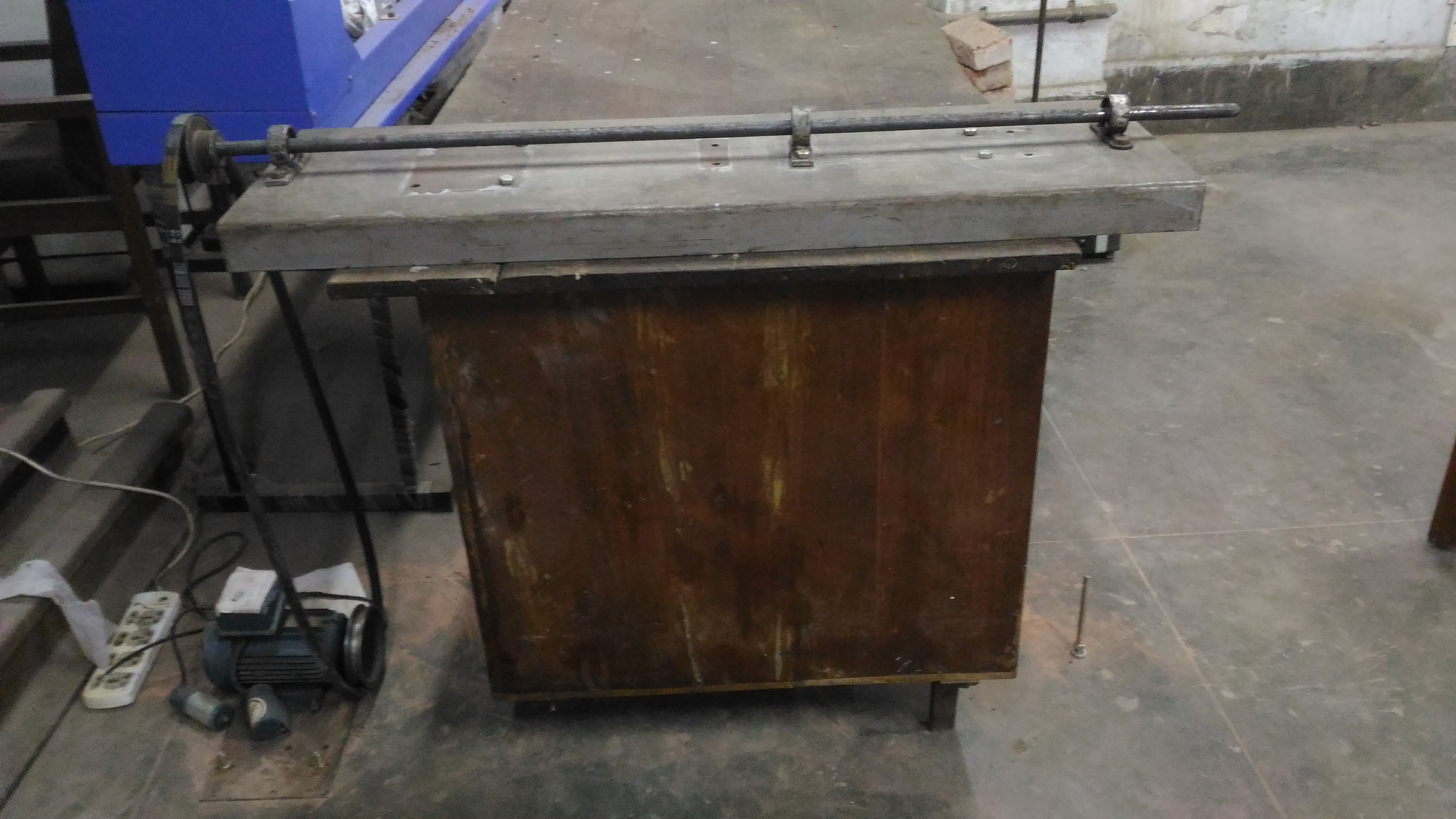
ANALYSIS OF INTERNAL DAMAGE OF BEARING
(Undergraduate Project 2018; term 4, Level 1&2)A novel approach of combining MEMS accelerometer and HFRT based bearing vibration monitoring system was tested experimentally to find out the internal damage of SKF 6203 bearing.
- Material- Bearing, Shaft, 1/2 HP Motor, Spring gaugge, Rubber belt
- Software- Solidworks, Arduino
My Responsibilities: CAD design, Developing physical Structure, Data collection and Report writing.
Professor-Department of Mechanical Engineering, BUET
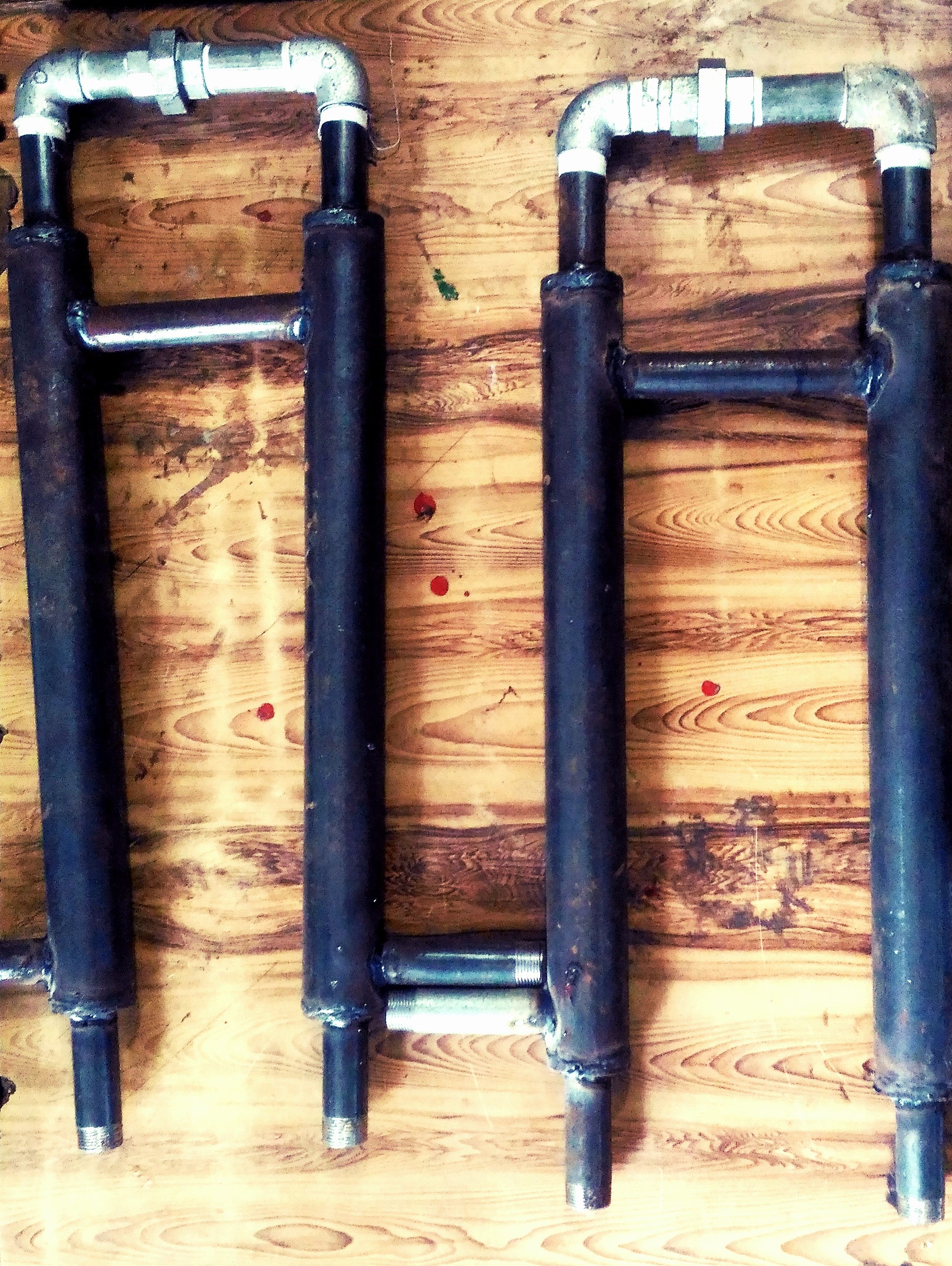
DOUBLE PIPE HEAT EXCHANGER
NOVEMBER 2018 (Undergraduate Project; Level-3, Term-2)The project is focused on developing an inhouse heat exchanger. Double tube heat exchangers are one of the most used in industries, research facilities and others. We fabricated this heat exchanger to analyze the physical phenomenon of the flowing fluid and the heat transfer of the tube shell during operation. AutoCAD was initially used to provide design to the local mechanics to build the prototype. Also, we used 3E plus software to calculate the costings before manufacturing. SOLIDWORKS was used as the software for designing the physical model and for the thermal calculations necessary for design optimization we used HTRI. In this project, the inlet, outlet and film temperatures of different flowing fluids in different chamber were calculated. Moreover, the pressure drop in inner shell, mass flow rate, heat transfer, shell conductivity, fouled heat transfer coefficient was analyzed in our project.
My Responsibilities: CAD design, Communicated with local mechanics, Data analysis, and Report writing.
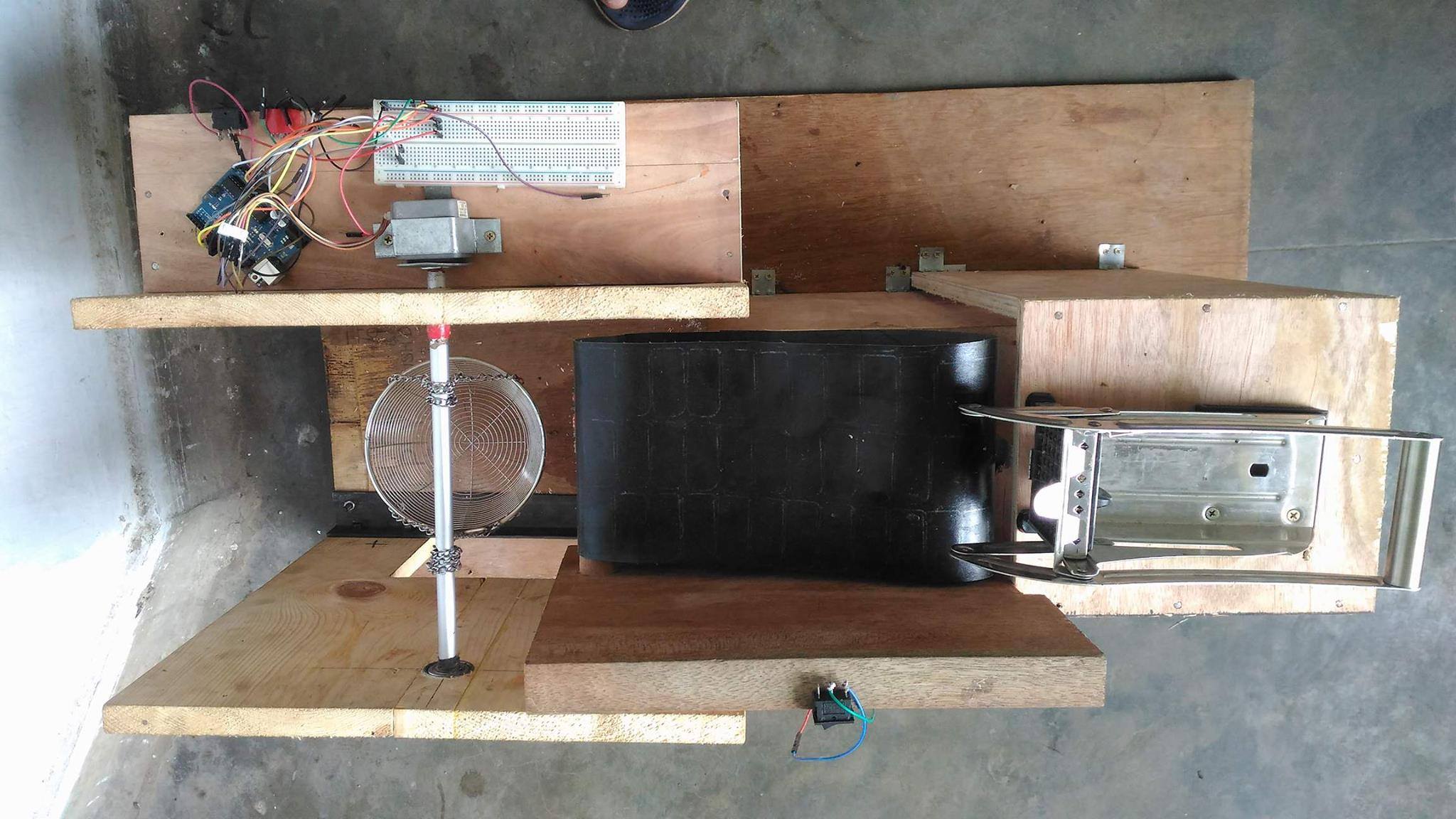
AUTOMATIC FRENCH FRY MACHINE
FEBRUARY 2018 (Undergraduate Project; Level-3, Term-1)- Software- Arduino, SOLIDWORKS
- Components- Wood Structure, Heater, Iron Chain, Servo Motor, Potato Cutter, Trade Mill
- In this project, we made an automated cooking equipment which saves time and manual labour
- Process- The potatoes are cut by the manual cutter,
then the slices fall on the trade mill that follows to the frying pan and were fried in a calculated time
My Responsibilities: CAD design, Developing physical structure, and Report writing.
A Cost effective model of 4 Wheel Steering
October 2017(Team Lead)
- Model Design by Solidworks
- Made the whole structure
- Selected for MEchaThon Competetion from BUET Campus
My Responsibilities: Collaboration of all individual tasks.
Ex Lecturer, Dept. of Mechanical Engineering, BUET
Line Following Robot
- Designed a line following Robot
- Software: Arduino
- Participated in a Robotic Competition at the Military Institute of Science and Technology, Bangladesh
My Responsibilities: Purchasing electric devices and Presentation.